With a rich legacy beginning in 1847, it is challenging to overlook the significant moment when Louis-François Cartier took charge of his mentor Adolphe Picard’s workshop at 29 rue Montorgueil in Paris, initiating an era of 177 years filled with opulence. In its infancy, the maison concentrated on creating jewelry for a distinguished circle of royal patrons. However, it was not until 1904 that Louis Cartier, grandson of Monsieur Cartier, crafted the brand’s first wristwatch — the Santos — for his aviator friend Alberto Santos-Dumont.
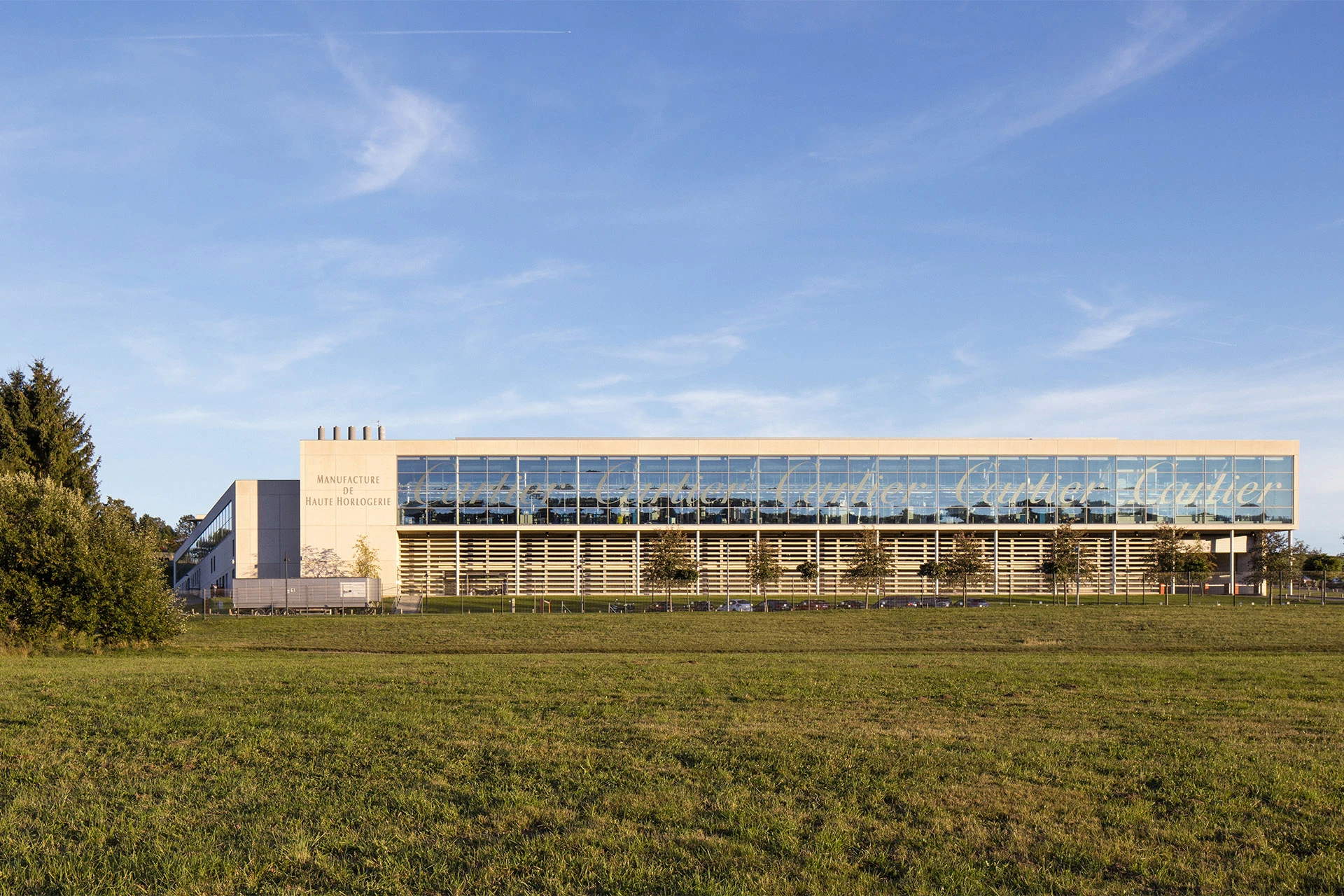
Though the watch was designed as a practical instrument for Santos-Dumont, Louis Cartier could not have foreseen its emergence as a central symbol of Cartier’s legacy and a catalyst for the brand’s evolution. The impact of the Santos watch expanded over time, leading to the introduction of other iconic timepieces such as the Tonneau, Tortue, and Tank. The growing demand for Cartier watches over subsequent decades ultimately spurred the need for a dedicated manufacturing facility, which finally began operations in 2001. Additional facilities in nearby Swiss Cantons contribute to the larger Cartier Watchmaking Manufacture. The watchmaking journey starts at Glovier, located in the Jura region, with steel and gold watches crafted and assembled in Villars-sur-Glâne, in Fribourg canton, while Cartier’s innovative technologies are trialed in Couvet. The Maison des Métiers d’Art, located in a renovated farmhouse nearby, is a short distance from the La Chaux-de-Fonds facility.
Situated in the center of La Chaux-de-Fonds, Switzerland, the Cartier Manufacture stands as a testament to unmatched craftsmanship and innovation. It is surrounded by the esteemed presence of other luxury brands, including Patek Philippe’s Crêt-du-Locle facility, the Greubel Forsey workshop, TAG Heuer, and Breitling’s manufacturing hub, as well as La Joux-Perret. At the dawn of the new millennium, this facility marked a significant chapter for Cartier, uniting various functional divisions such as design, manufacturing, assembly, and support under one roof. The importance of the Cartier Manufacture extends further as the combination and concentration of traditional craftsmanship and modern technology breathe life into the renowned Cartier watches.
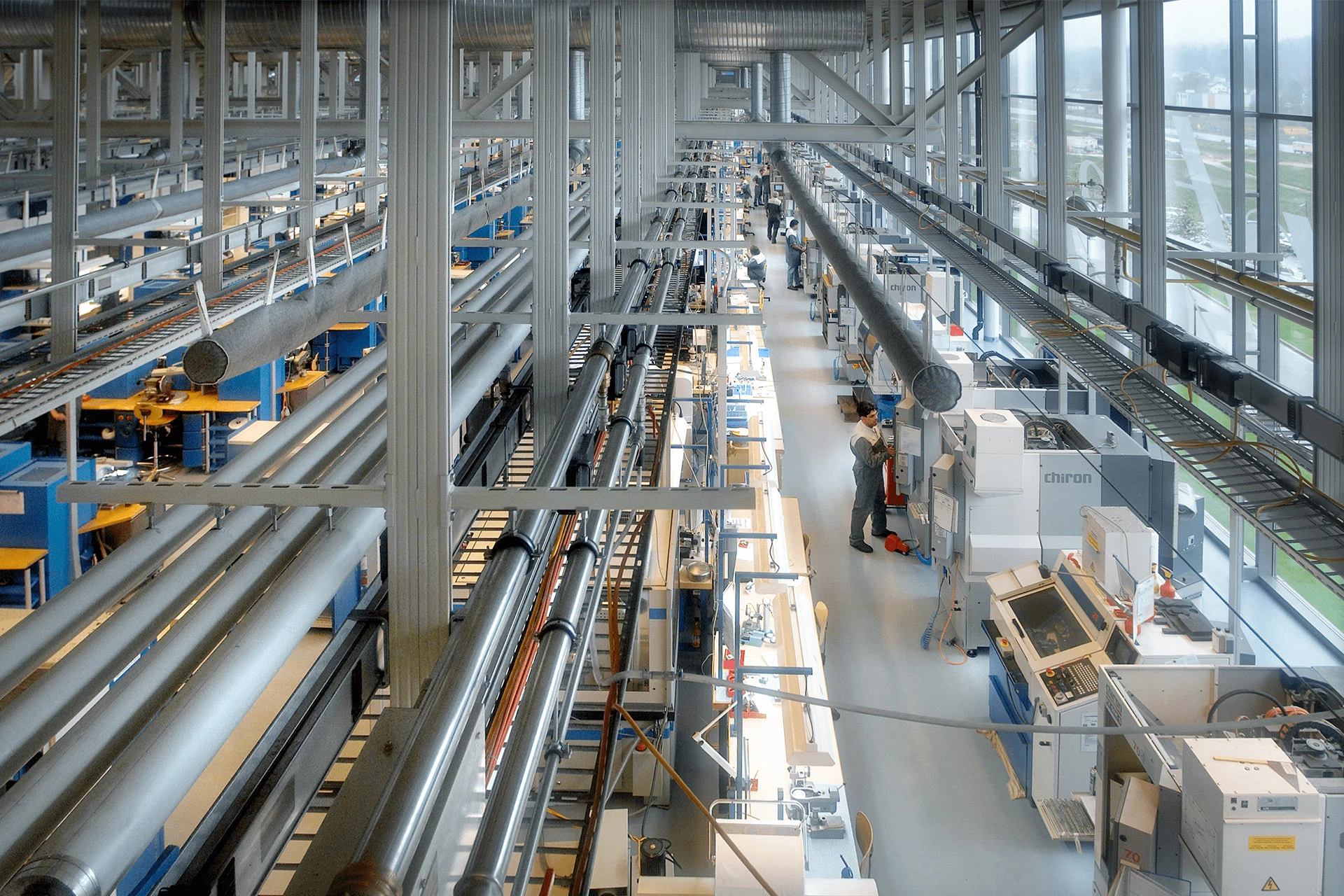
In contrast to dilapidated or dusty workshops, the Cartier Manufacture features a cutting-edge space of 33,000m2, appropriately segmented for various departments behind its steel and glass exterior. The first level accommodates heavy machinery, including CNC equipment, while a cleanroom with environmental controls contains the calibration assembly and quality inspection teams. Other departments at the manufacture include restoration, quality control, design, polishing, and assembly teams.
From Paper to Metal
The journey of a Cartier watch begins with a fleeting idea — often more intangible than tangible. Just as images convey complex messages, a sketch is the best way to communicate an idea. Using input from the marketing team, designers illustrate and transform these concepts into sketches from varied perspectives. This is where imagination and creativity flourish. Gouache (an opaque watercolor) enhances the sketches by introducing colors — such as colored gemstones set on a yellow-gold casing and bezel — into an otherwise monochromatic world. Notably, during the eight years under the leadership of the recently-departed CEO and current chairman of Cartier Culture & Philanthropy, Cyrille Vigneron, every sketch — whether meant for standard production or custom client orders — required his personal endorsement. A signature at the bottom right approves the design team to advance to prototyping, or the sketches must return for further refinements.
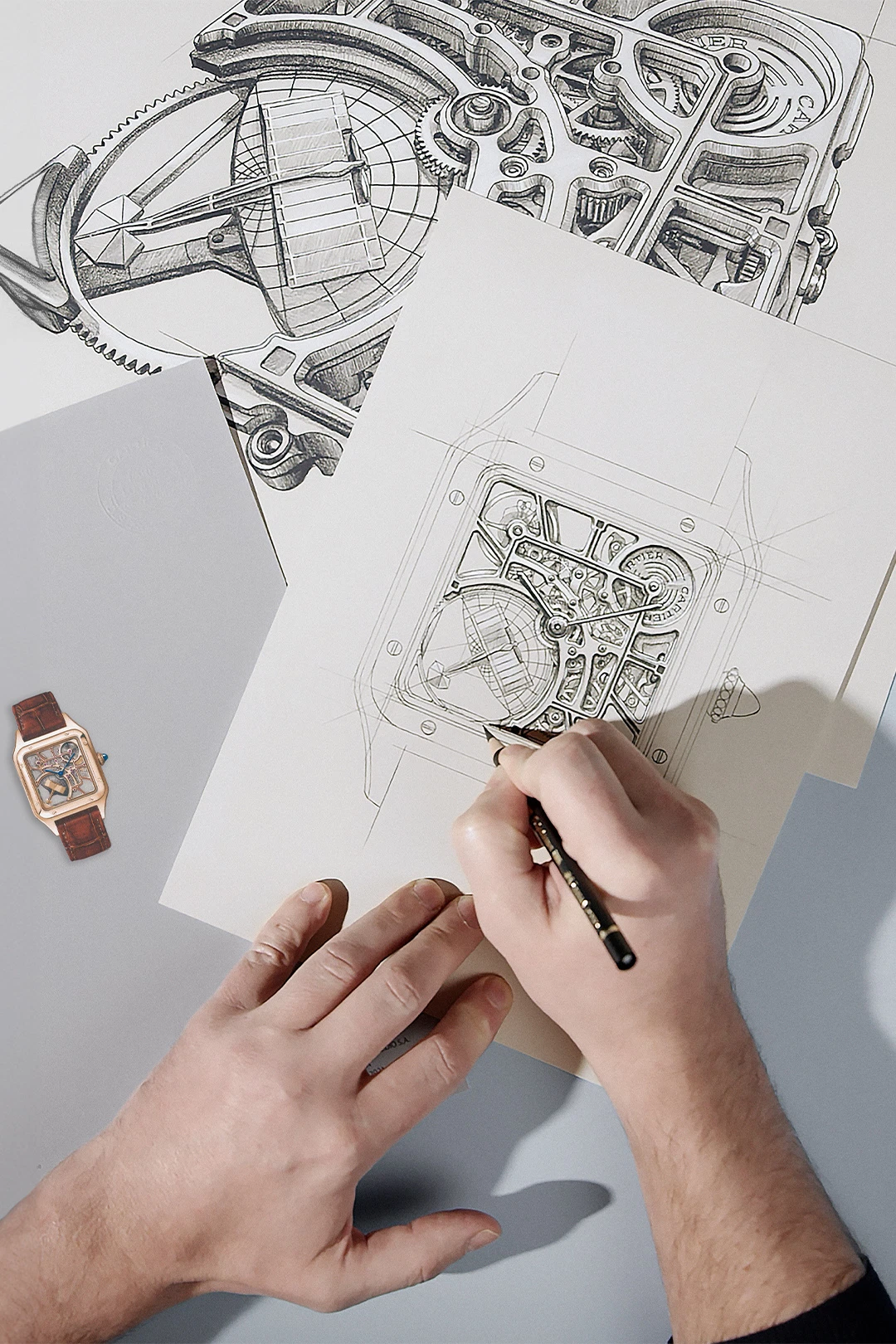
Following this, resin prototypes are crafted using 3D printing technology. This enables the development teams to evaluate the watch’s aesthetics, such as the contours of the Ballon Bleu de Cartier or the flexibility of the Pasha de Cartier’s bracelet before actual working prototypes are produced based on detailed technical documentation. This documentation is vital to the production process since the required expertise and skills help systematically define and outline manufacturing procedures. Moreover, it facilitates the simulation, review, and fine-tuning of these processes to meet specified production quantity requirements as they are established later.
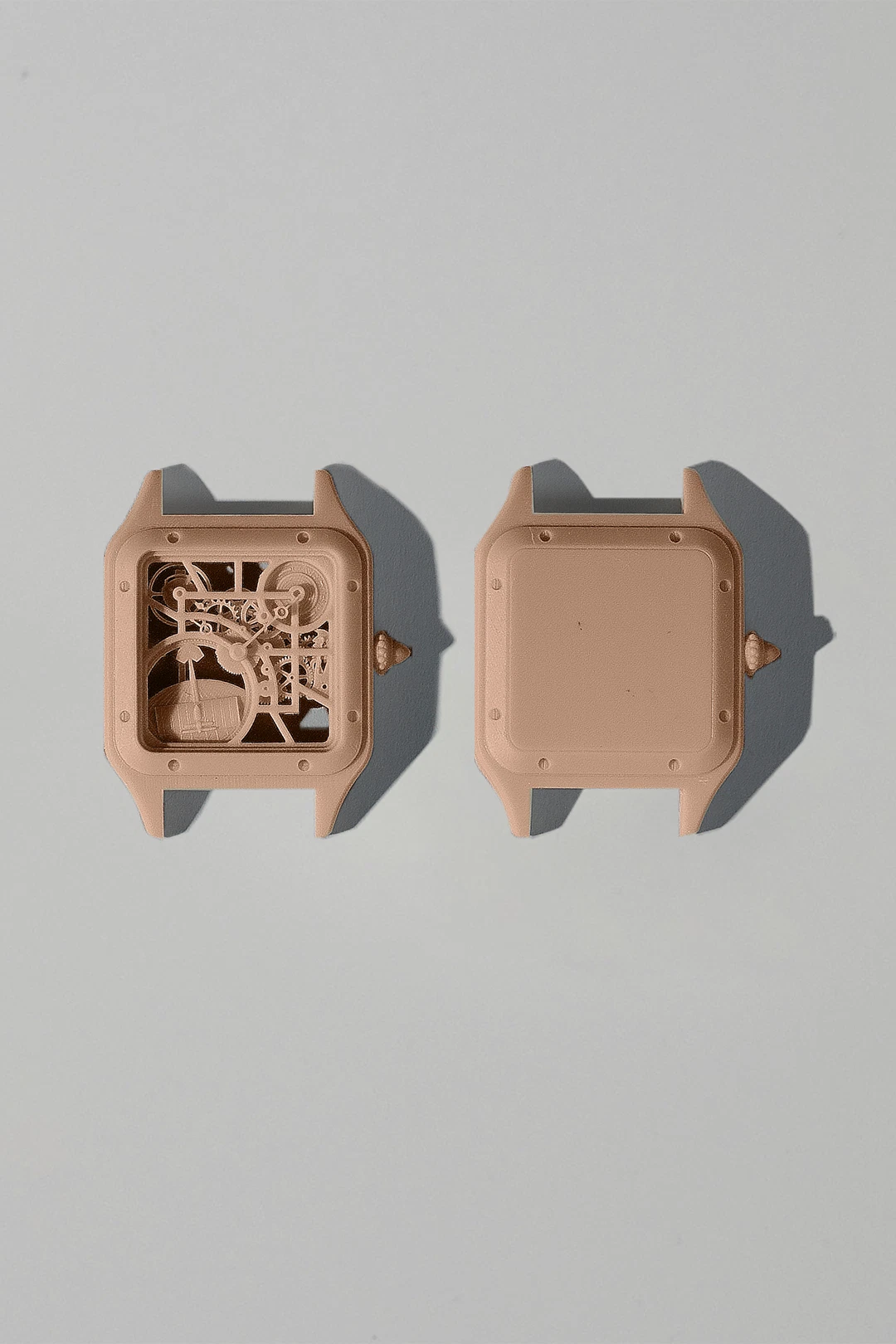
As we explored the facility, several fascinating areas caught our eye, showcasing both traditional and innovative techniques. On the traditional end of the spectrum is the mineral crystal shaping team, which — according to Cartier — represents a nearly lost art in Switzerland. Because many Cartier watches feature unconventional shapes — like the Baignoire or renowned Crash — mineral crystals are used in place of sapphire crystals, thanks to their adaptability to fit various models. Rather than relying on machinery, an artisan manually shapes the mineral crystals using a blowtorch until they can be molded to the specifications of different watch designs. Inspections are conducted through human observation, not machinery.
On the opposite side, specialized machinery for specific tasks, including milling and CNC devices in the bracelet manufacturing sector, plays a crucial role. These machines shape bracelet links from solid metal bars. Up to nine bars can be processed at once, with the simplest bracelets taking about 30 seconds per link, while more intricate designs may require up to 90 seconds. Given Cartier’s commitment to quality and reliability, inspections are conducted throughout manufacturing. An automated four-step test immerses the watches in water and acid, and exposes them to magnetic fields and extreme temperatures to ensure they can withstand these elements. To guarantee the durability of its watch bracelets, Cartier employs a machine dedicated to stress-testing, simulating extreme wear to evaluate their structural integrity.
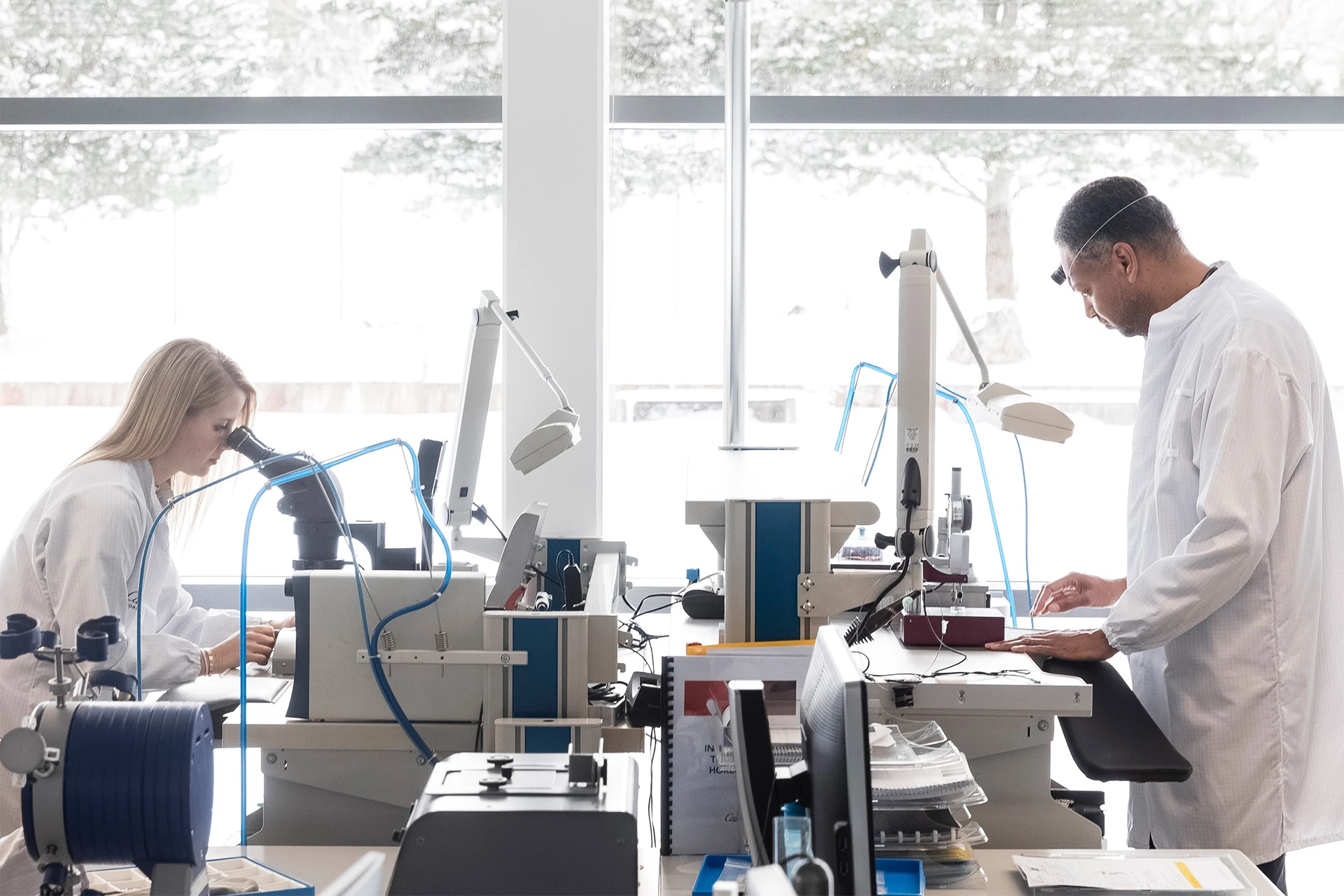
At a midpoint on the spectrum lies Cartier’s restoration department, responsible for rejuvenating vintage Cartier watches and clocks. This highly specialized team represents one of the highest achievements of Cartier’s watchmaking prowess, as skilled artisans bring ancient pieces back to life. Whether through cosmetic or mechanical restoration, the team uses a range of methods, from accurately reproducing period-specific components sourced from archival blueprints to overcoming certain challenges with creative solutions.
Where Splendour and Dreams Come Alive
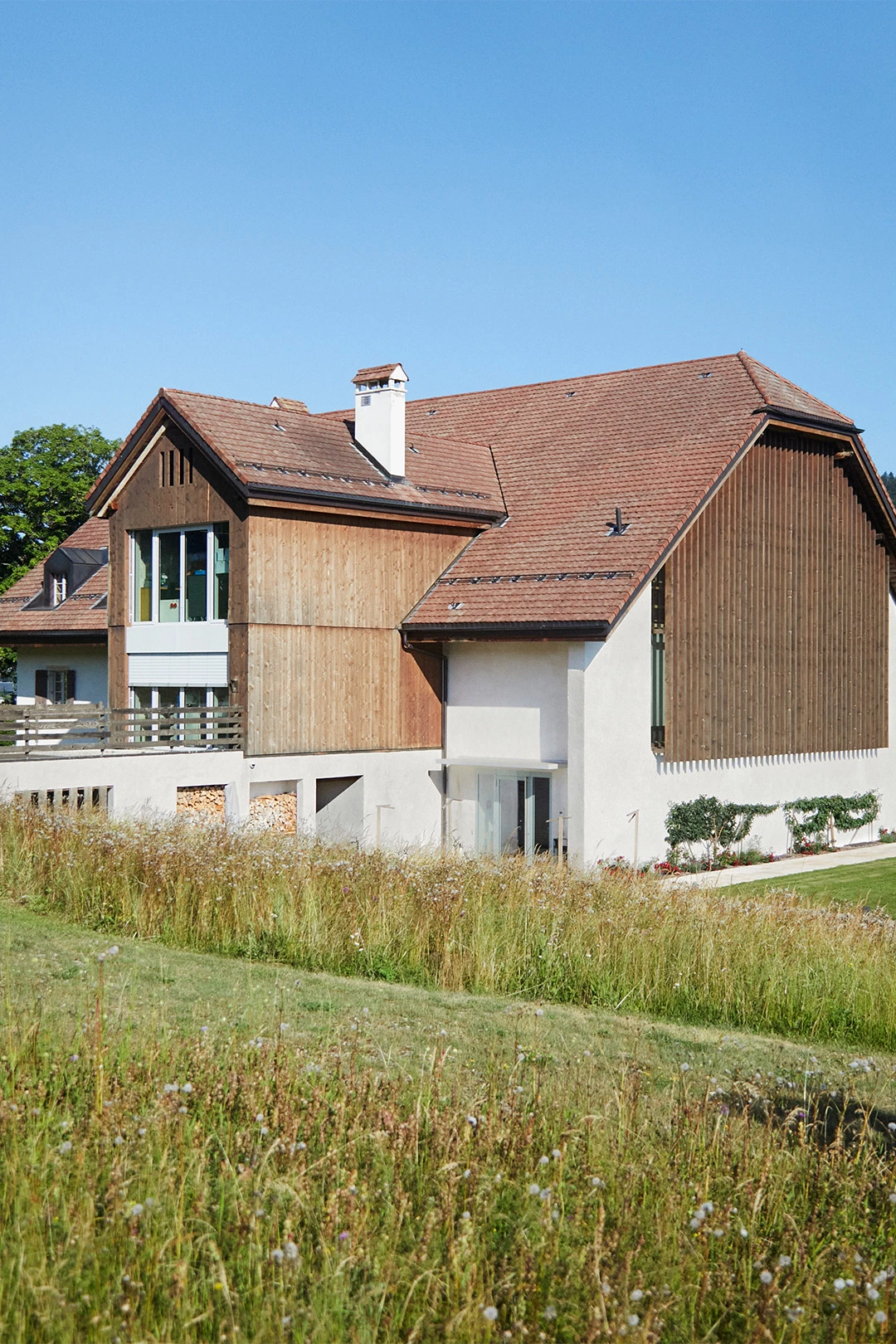
Opened in 2014, Cartier’s Maison des Métiers d’Art is located close to the Cartier Manufacture. Unlike the sleek design of the Cartier Manufacture, it occupies an old farm. Within its venerable walls lie even older artisanal skills, rich with tradition, heritage, and inherent secrets, brought to life through limitless creativity and imagination. Time appears to warp within the atelier, as these ancient methods are adapted and woven into modern interpretations that challenge conventional beauty standards. The numerous developed techniques can be broadly categorized into three main areas: the artistry of fire, metal, and composition.
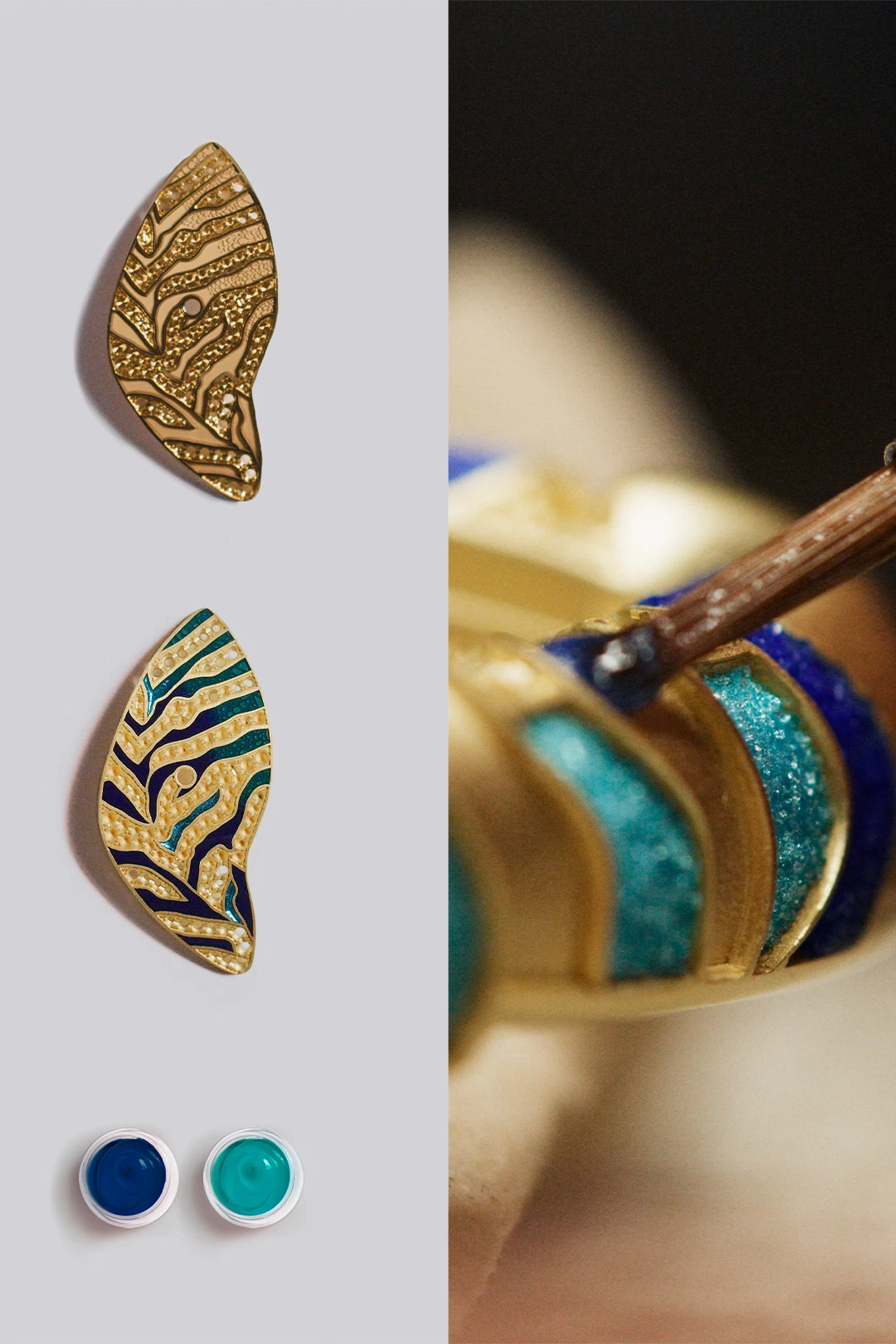
Enameling — belonging to the art of fire — is a well-known technique. Cartier’s expertise spans various methods, including, but not limited to, champlevé, cloisonné, plique-à-jour, and grisaille enameling, which deserve recognition. Enamel begins as colored glass powders in paint form and undergoes multiple firings in kilns (up to ten rounds of painting and firing) at varying temperatures to cure or vitrify it. While enameling primarily features on watch dials, the Cartier Crash Tigrée Metamorphoses showcases enamel on its bezel. In this piece, artisans extensively applied enameling to enhance or sometimes complement other artistic techniques. Various hues are masterfully rendered through opaque, translucent, or graduated enameling on surfaces like silver paillettes or in engraved grooves of the stripes (known as champlevé enameling). The blues and greens used in this piece are created using cobalt oxide (for blue) and copper oxide (for green).
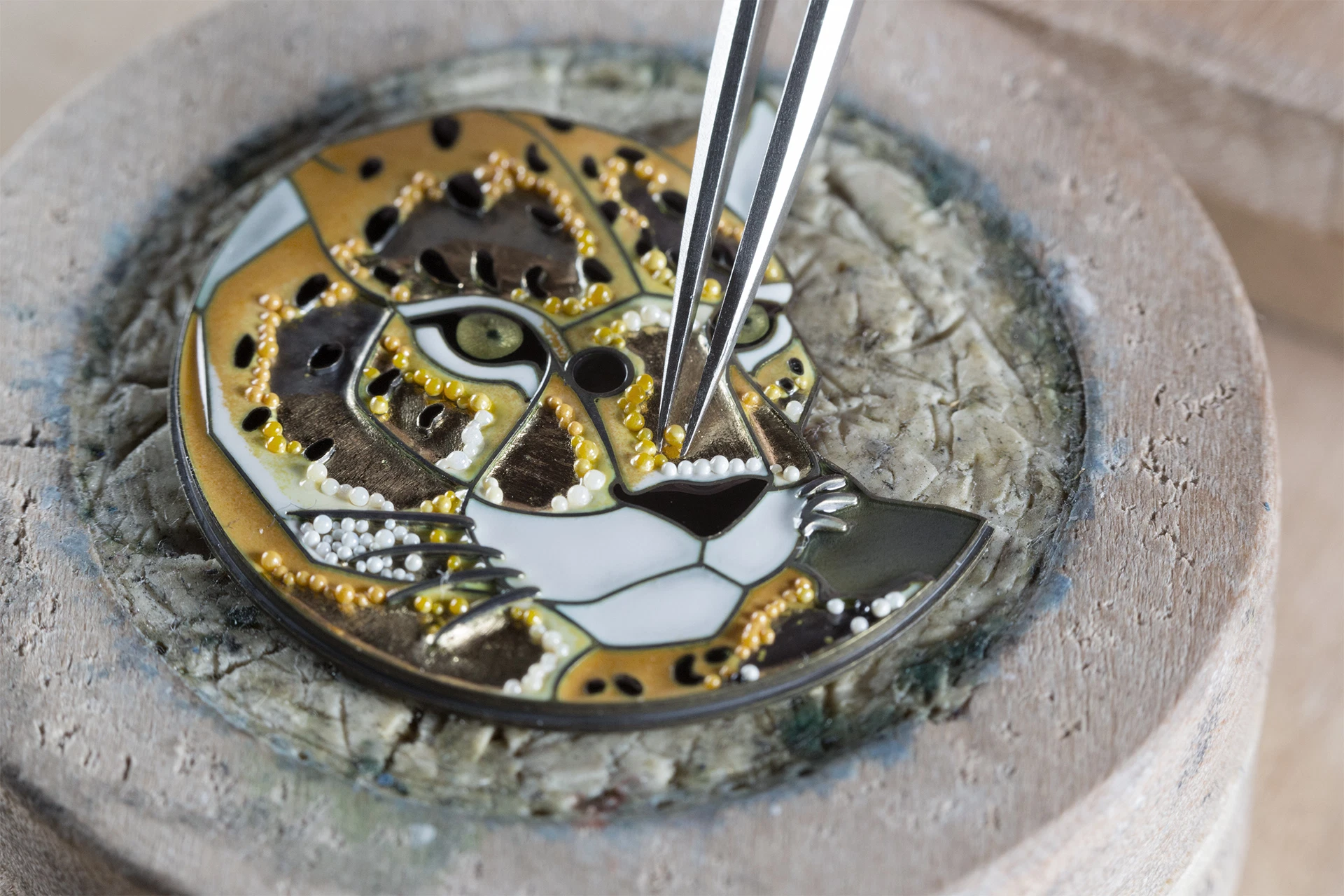
Etruscan granulation, filigree, and flamed metal techniques are classified under the art of metal. The former technique, which dates back to 4 BC, was popularized by the Etruscans and involves tiny beads that embellish jewelry surfaces. Gold wires are heated before being cut into small pieces and placed into crucibles filled with water. Rapid cooling causes the gold fragments to form spheres, which are sorted by size. Soldering these beads into decorative patterns is the most conventional application; however, utilizing a viscous liquid with sapphire dividers and gravity to construct the outline of the panther’s head featured in the stunning Révélation d’une Panthère exemplifies the maison’s innovative spirit.
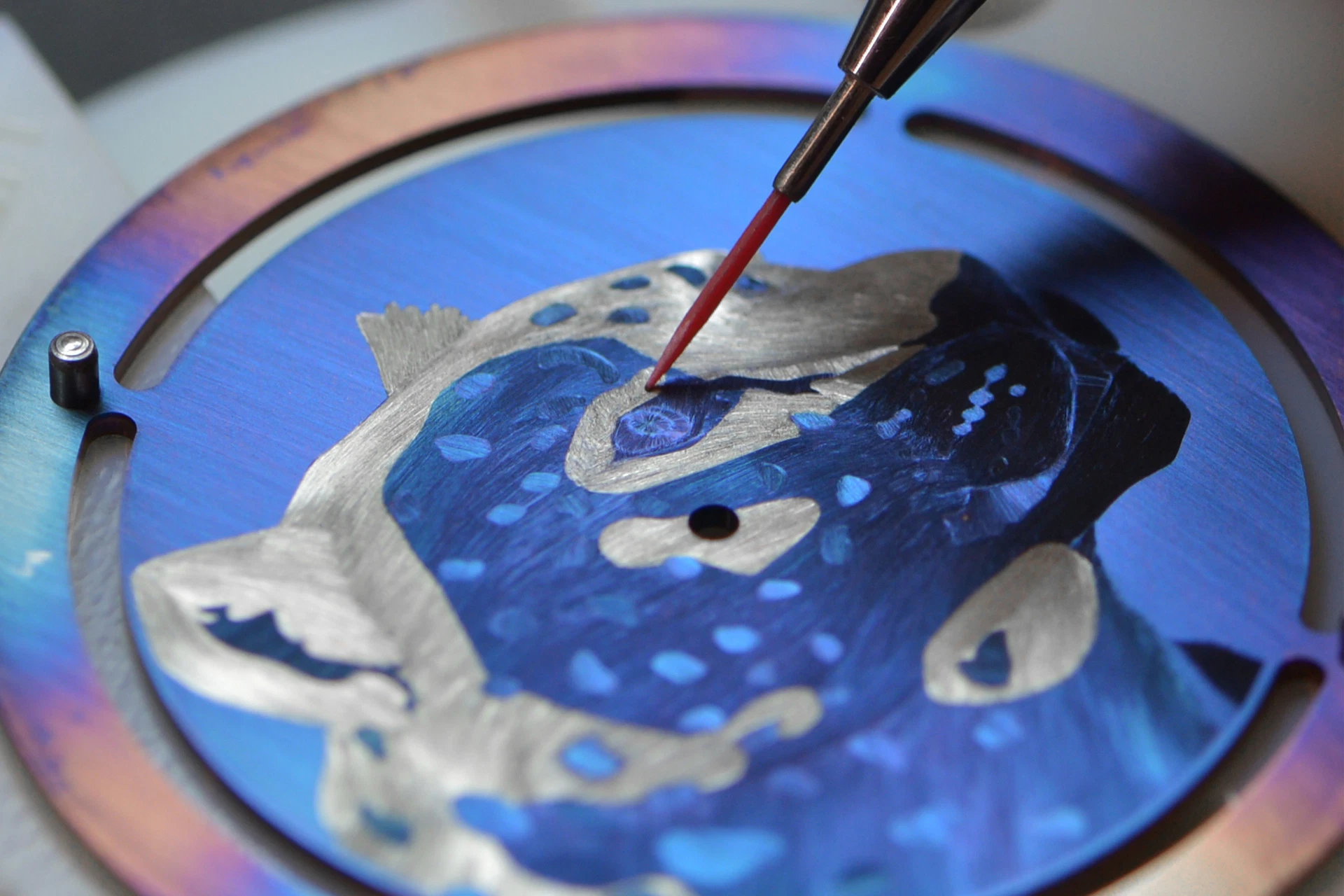
One of the newer Métiers d’Art techniques within the department is flamed metal, which involves heating metallic surfaces to achieve various colors through oxidation. The process starts by uniformly heating the dial plate to create a blue hue, after which unwanted areas are scraped away to form Cartier’s iconic wildlife motifs. Artisans mask the blue portions before reheating the dial plates to produce shades of brown ranging from beige to dark brown. Due to the irreversible nature of such oxidation, the technique becomes increasingly challenging in the later stages of the firing. An expert eye and deep understanding of the craft are necessary to know the precise moment to cease the firing. Cartier’s final art of composition is perhaps the most unique, intricately combining mosaics and marquetries of wood, straw, flowers, and gold to create exquisite watch dials. Seemingly random shapes and colors are harmoniously arranged to create either abstract or lifelike themes.
As the Maison des Métiers d’Art celebrates its ten-year milestone, artisans remain dedicated to creating beauty, unified in their mission to preserve, innovate, and share their exceptional expertise. With some techniques previously on the verge of extinction, there is optimism that these time capsules of the past will be safeguarded and passed down through generations to come.
This article initially appeared in Mens Folio Singapore.
For more updates on luxury watch literature, click here.
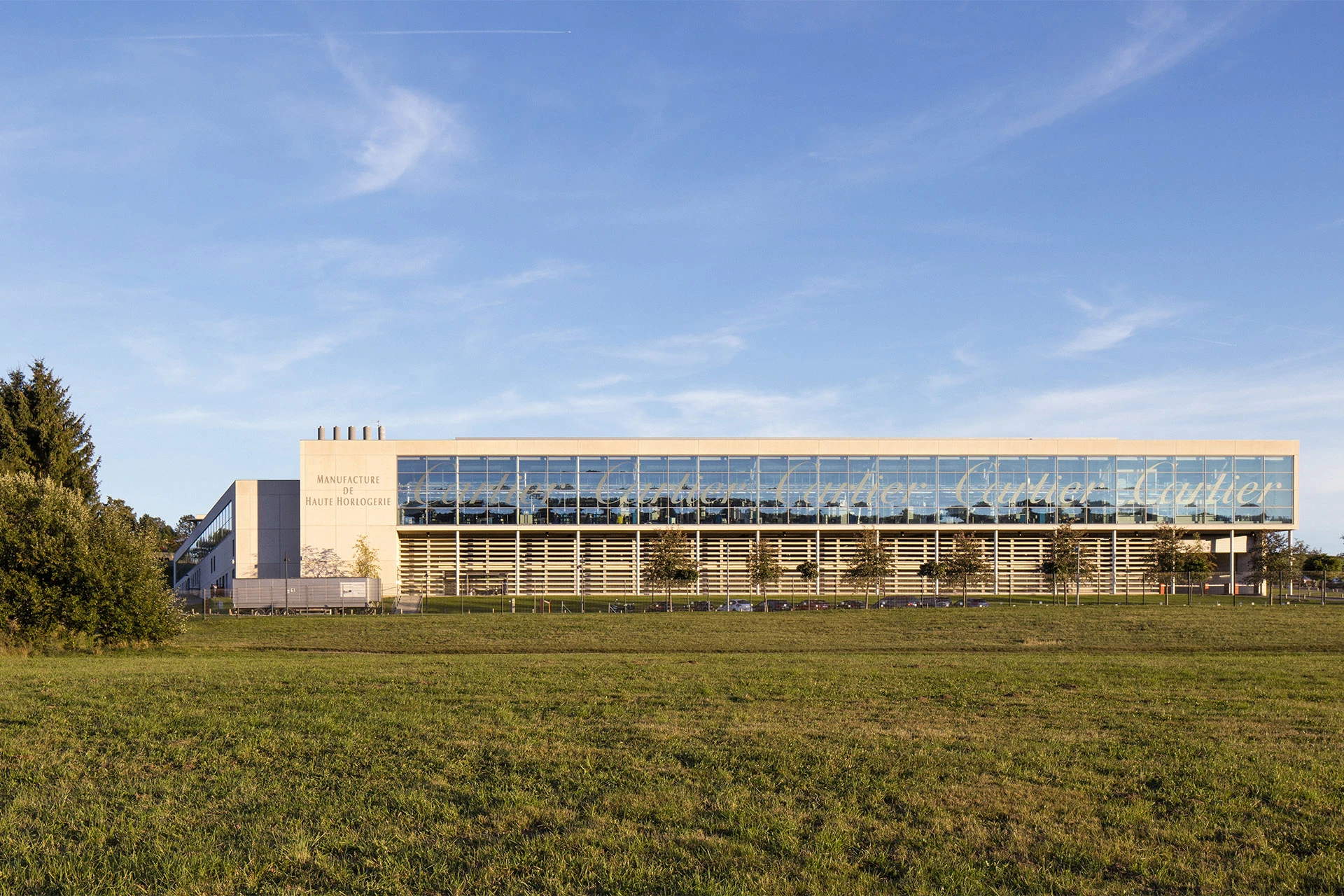
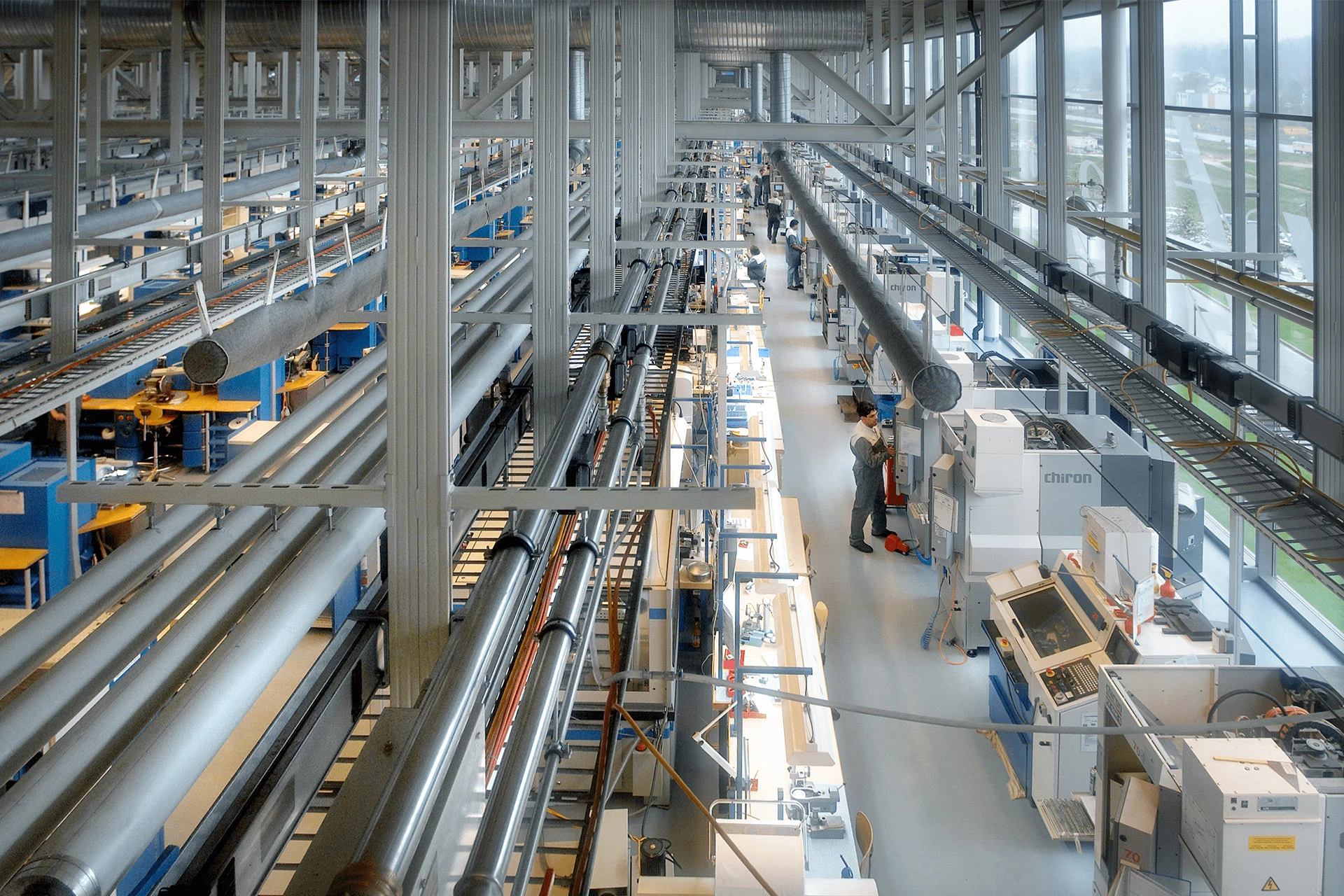
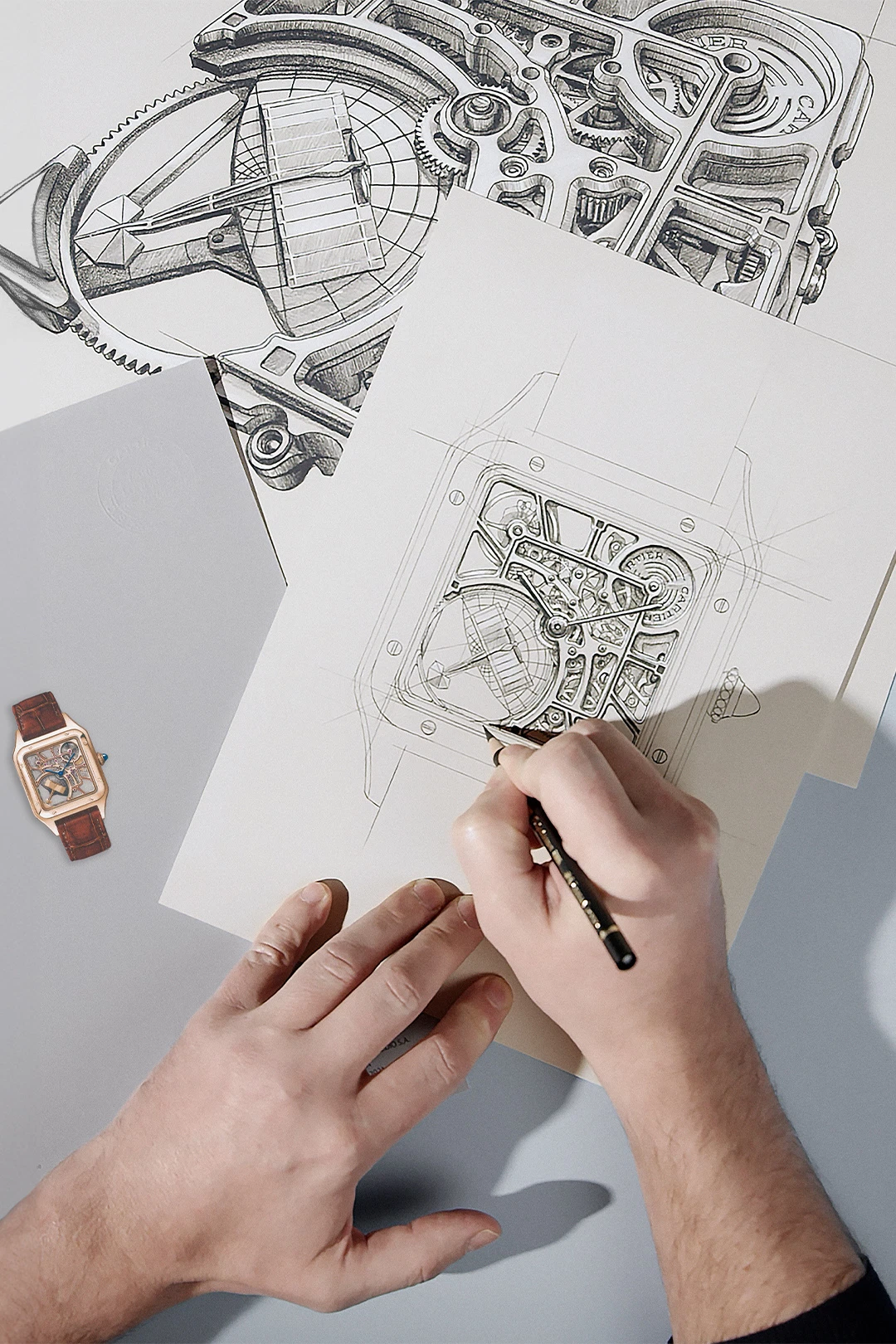
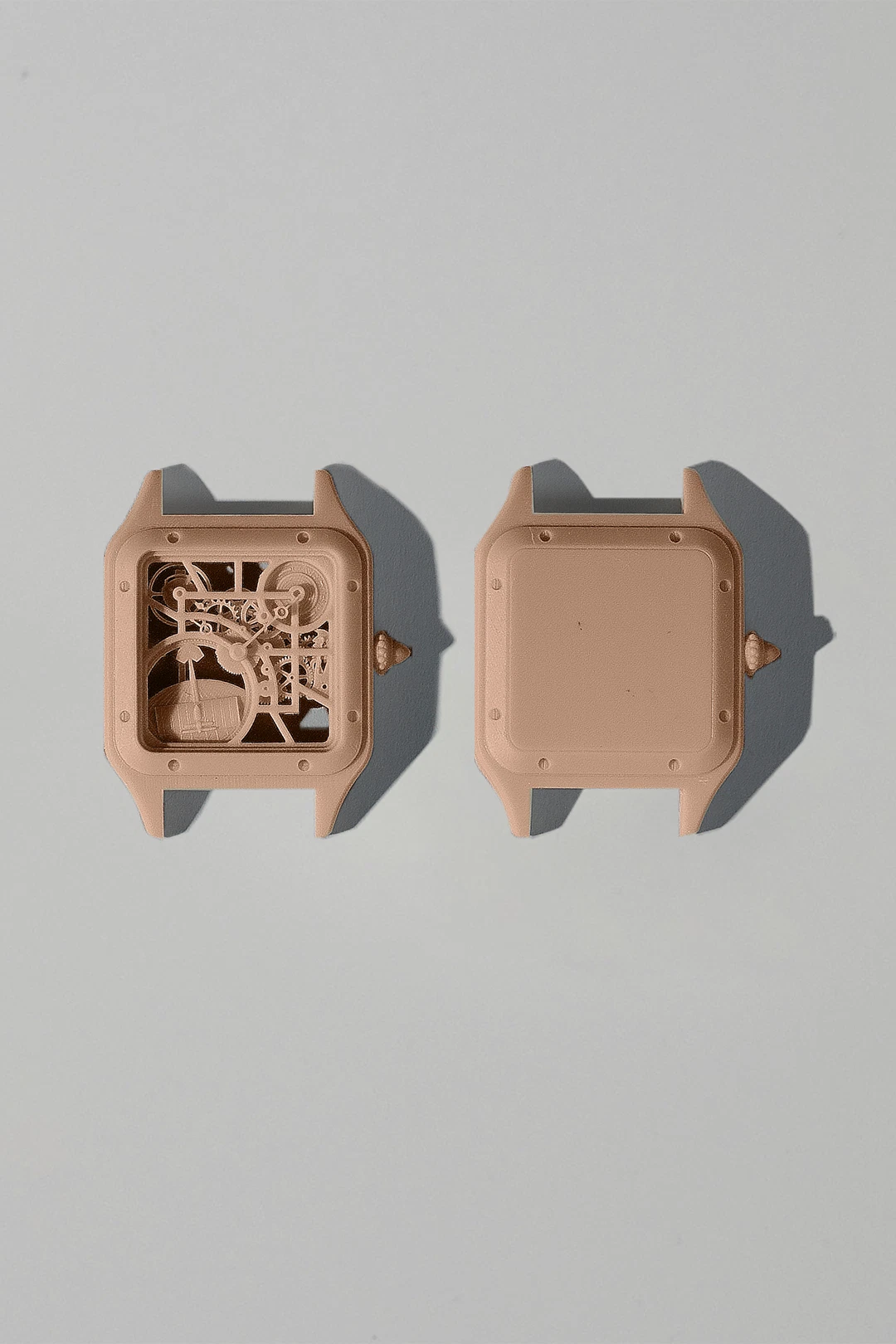
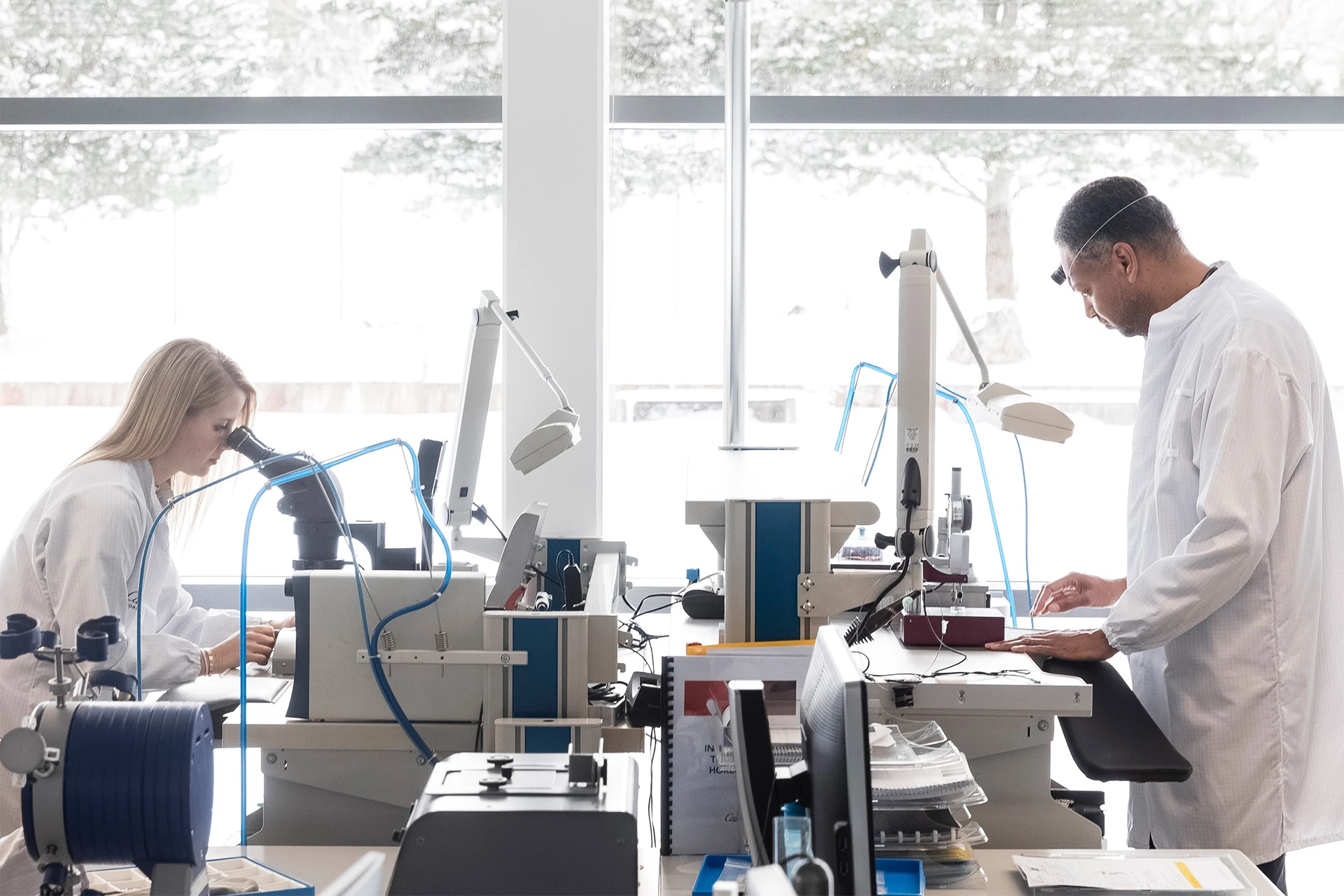
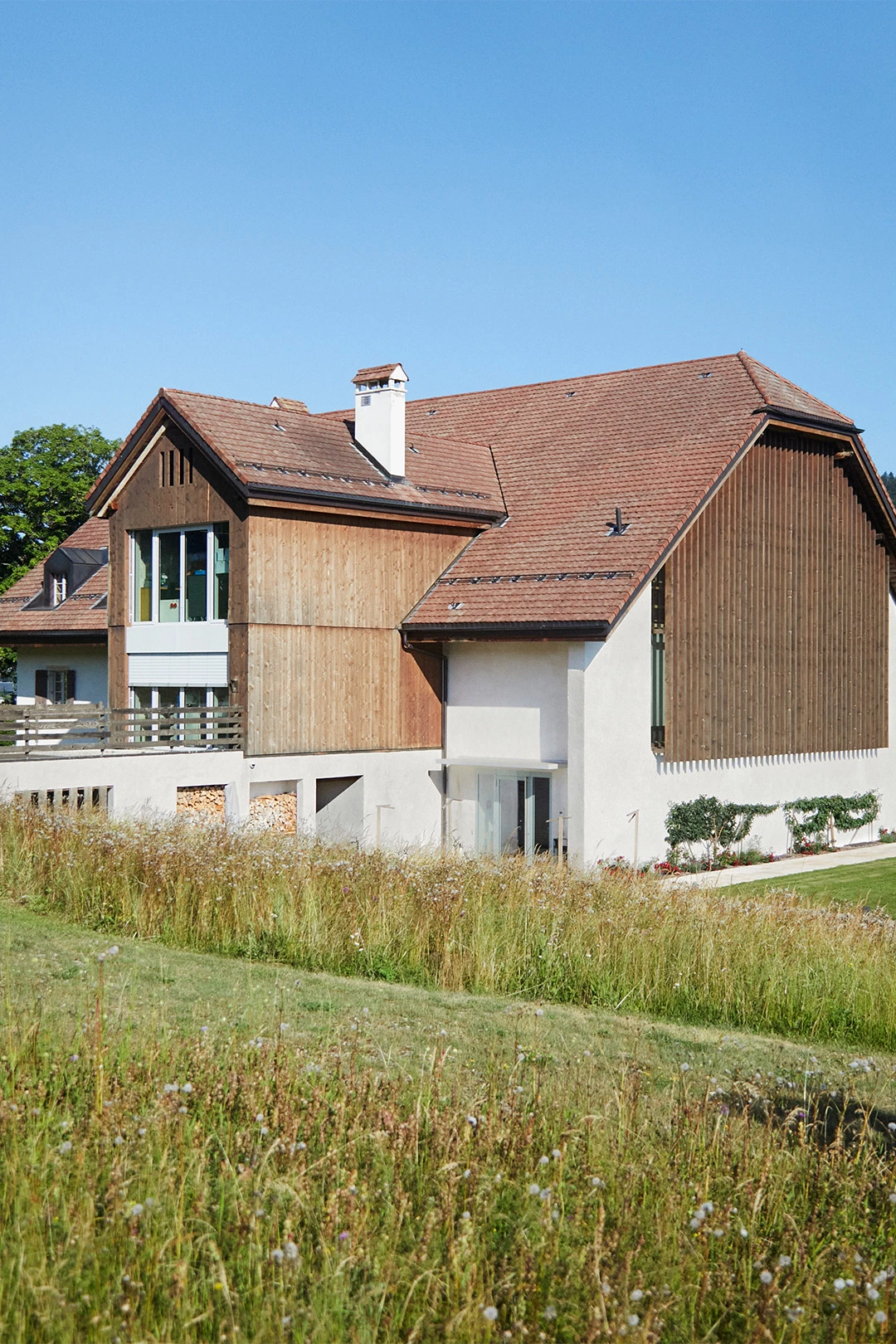
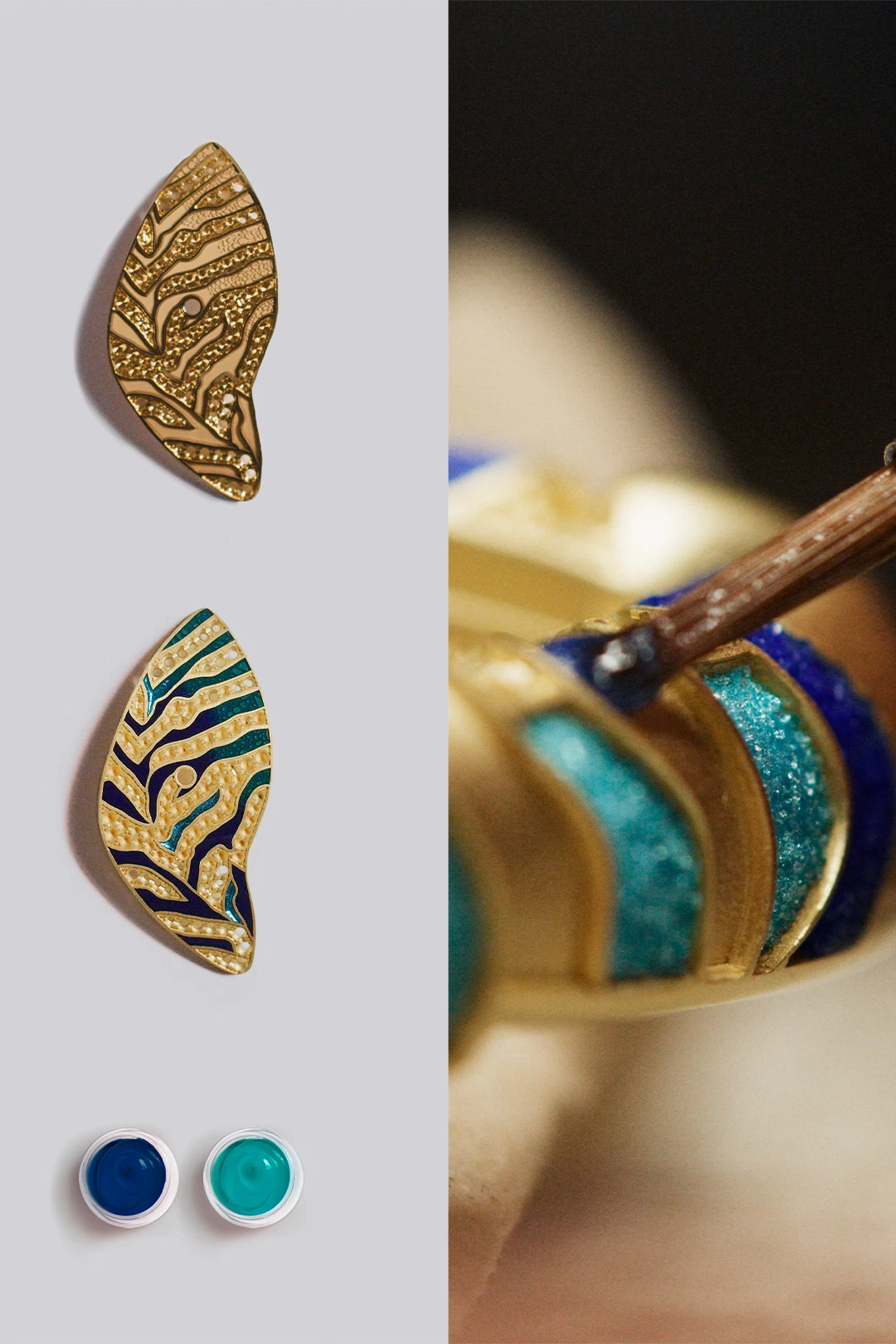
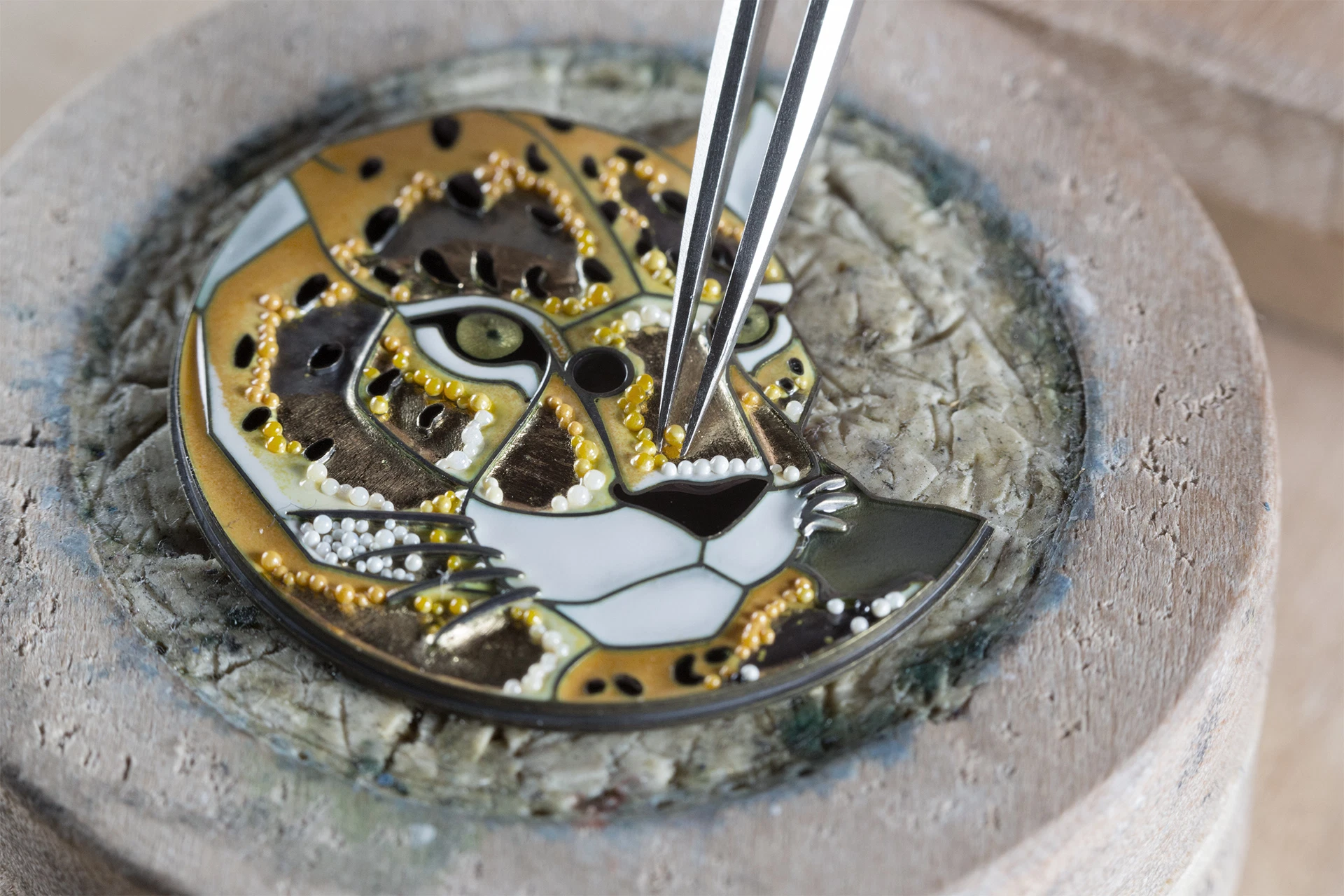
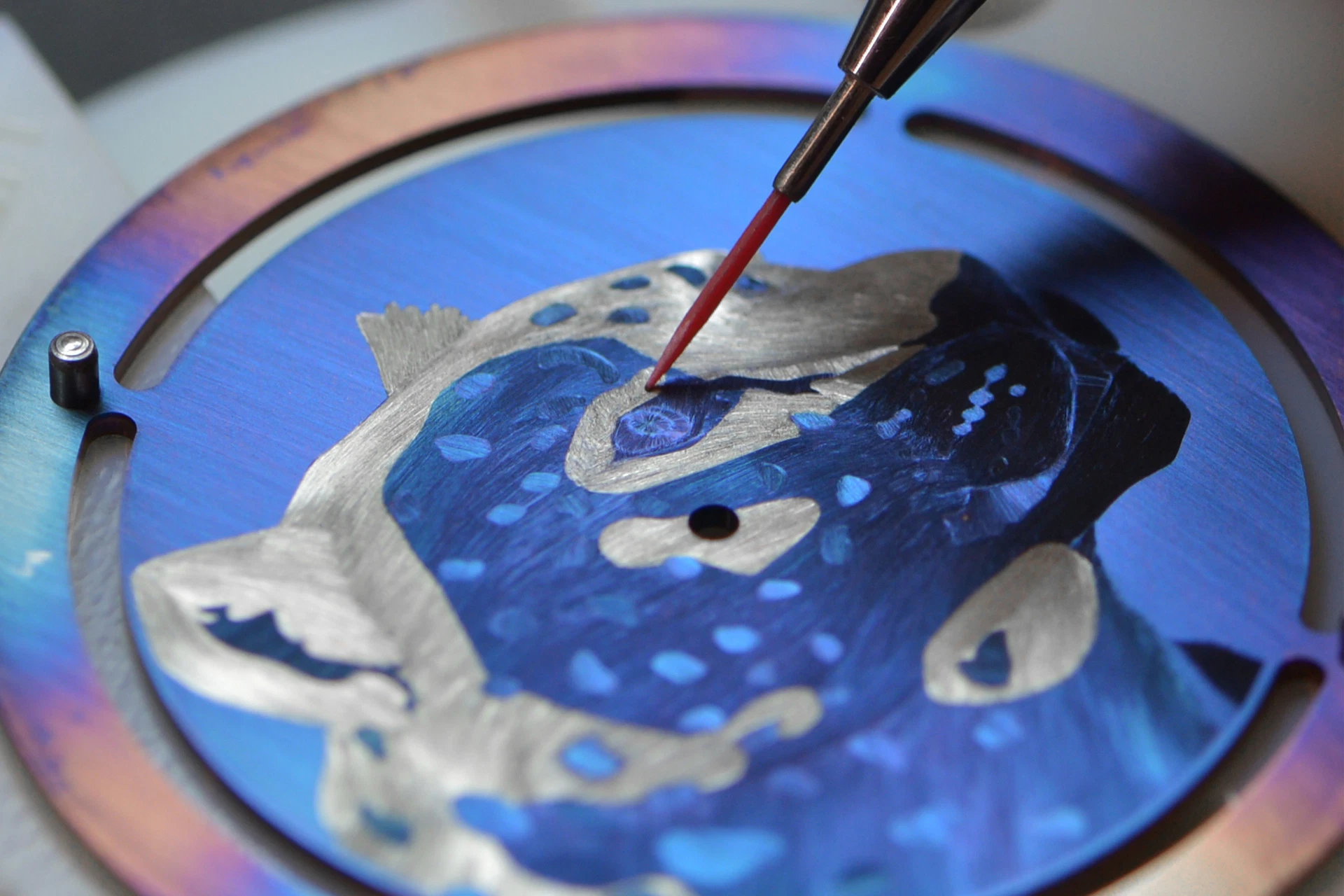